Floor Installation Instructions
Floor Installation Instructions
Stile® Porcelain tiles are installed similar to other porcelain products. Stile® porcelain tiles are available as 118” x 59” x 6 mm and in 126”x63” in 6 and 12mm. Tiles can be used full size for flooring or cut to any required size. Successful Stile® Gauged Porcelain Tile floor installation is achieved with a proper subfloor, binding layer and expansion joints.
For visual details, watch our flooring installation video here.
The environment where tile is installed is critically important to successful installation and continued performance. The area should be free of all construction debris, dirt and surface contaminants.
Always consider the potential adverse effects of extreme temperatures and humidity on mortar and grout with exterior installations of Porcelain tile. Adequate ventilation, heating and/or air conditioning should be available to sustain an environment required for the installation of bonding and grouting materials. The type and methods of construction, grade level and flooring system components all impact the final installation. Some minimal code requirements for flatness, levelness and deflection may not provide a suitable system for the installation of Gauged Porcelain tile flooring.
Concrete and Masonry – When large porcelain slabs are directly bonded to an existing concrete or masonry substrate, the installation is greatly affected by the suitability and condition of the concrete or masonry supporting the installation and providing the bonding surface. Flatness of the substrate must be checked to meet industry methods and specifications.
If substrates do not meet the flatness requirements and remedial corrections are not made, the installation will likely have lippage or flatness issues.
Wood Substrates –Wood is not a recommended substrate as it expands and contracts when its moisture content changes. Wood substrates deflect, or bend, under loads more than concrete substrates.
Stile® Porcelain tile installations require a rigid substrate that will not deflect or bend when loads are applied.
Backer boards are suitable underlayments to install over a wood subfloor to receive large porcelain slabs. There are several types, each having different application suitability and some unique installation requirements for different applications.
Once your surface is prepared, you will need to lay out the tiles on the floor before they are installed.
Layout is critical to an aesthetically pleasing tile installation. Tile layouts should be centered and balanced as much as possible with respect to the tiled area and any specific focal points. Usually, a space offers more than one acceptable layout, making the final selection a matter of personal preference.
To start planning the layout of your tile, you must first find the center point of the room. To do this, measure the four walls in the room and find their midpoint. Then, snap two chalk lines, one from the midpoints of two opposite walls and another from the midpoints of the other two walls. Where they intersect will be the room’s center point.
Check that the chalk lines are square by marking points 3 feet on one chalk line and 4 feet on a perpendicular chalk line starting at the intersection. Measure the diagonal space between each of these two points. If the distance between the two is exactly 5 feet, the lines are square. If the lines are not square, the tiles will not be centered and the room might look unbalanced.
If the room is not square — which is very common — you will need to make adjustments to the position of one line, and then square the other line using the 3-4-5 procedure.
Next, you’ll want to lay a single half row of tiles in both directions without mortar, starting at the center point and working outward. You do this to ensure the finished project will be centered.
Insert spacers between the tiles. Stop when there is not enough room for a full tile. If the space at the end of either row is smaller than one-third of a tile, you’ll want to adjust your chalk lines so half tiles appear on both sides of the room. Since you started in the center, one-third of a tile on one end means you’d have two-thirds of a tile on the other end and your room will look off-center.
After making any adjustments be sure to resnap new chalk lines.
When installing tile, be sure to wear safety glasses and rubber gloves when mixing and applying mortar. Also, consider wearing knee pads to evenly distribute your body weight and save your knees. You’ll be glad you did.
Read the mixing instructions on the back of the package to ensure proper mixing of the mortar mix. One more thing: When tiling an area that will butt up against a different kind of flooring, like carpet or hardwood, a threshold transition is needed. Check with one of our associates prior to your project to find out which type is right for your project and when it should be installed. Some go in before tiling begins and some are installed at the end of your project.
Thin-set mortar (LFT – Large Format Tile) is the cement or bonding agent used to attach the tile to the backer board or concrete subfloor. Use a large bucket and a drill with a mixing paddle. Be sure to clean the mixing paddle promptly so the mortar does not harden on it. Some mortars are labeled as “non-modified” and require a latex polymer admixture that will improve the performance of the mortar and increase bond strength. But most mortars come already modified.
Porcelain floor tile must always be installed using a polymer modified thin-set to achieve the appropriate bond between the tile and the substrate receiving the tile. This also applies to exterior installations.
Mortars must be allowed to stand for five to 10 minutes after mixing. They cannot be used immediately. Slake time, as this is referred to, allows the chemicals in the mortar to fully activate. Make sure you follow the instructions on your mortar mix package.
For wood subfloors where a backer board was installed, be sure to moisten the backer board by misting with a spray bottle filled with water before spreading the thin-set. Spray the backer board as you work. If you don’t do this, the backer board will soak up water from the mortar causing it to dry too rapidly. This will impact how well your tiles adhere to the subfloor.
Take care not to mix too large a batch of thin-set. It has a limited working life and if you’ve mixed too much it will start to harden before you’ve had a chance to use all of it. If this happens, you’ll need to discard it and mix more. Do not add water after the thin-set begins to harden because this weakens the cement and severely affects the bonding between the tile and the backer board.
Mix up a bucket of thin set mortar appropriate for the type of tile you’re installing. There are differences so check with a store associate to ensure you make the right choice.
Trowels have both a smooth edge and a notched edge. The notches are called teeth. A Euro or zipper notch trowel should be used when installing Porcelain Slabs. For all applications, both the back of the tile and surface where it will be installed need to have thin set applied to them. For floor applications, a 3/8” notch should be used. For wall and countertop applications, a ¼” notch should be used to spread the thin set to both surfaces.
Since you are troweling both surfaces you need at least three people on site. One person will be mixing thin set and assisting with the tile. The other two will be spreading thin set, one on the substrate and the other to the back of the Porcelain slabs. Make sure the tile is in place where it is to be installed as to keep moving it to a minimum since the thin set will add at least 50 pounds to the slab once it is applied. Stile® Porcelain Slabs should be handled with glass suction cups and stabilizer bar (or equivalent supporting system). The use of leveling spacers is required per the ANSIA108.19 specifications to minimize the amount of lippage in your finished floor.
To begin, ensure that your follow the mortar mixing instructions and consistency of the mortar is appropriate.
Once you’ve confirmed you have the right consistency in your mortar, spread thin set perpendicular to the long side of the tiles. The thin set must be spread to the substrate in the same direction. Once the thin set has been spread to both surfaces, the tile can be placed where it is to be installed. Be aware that due the size of these tiles and the amount of thin set applied, it will be very difficult to move once set in place. There is also a very likely chance of breakage. Once in place, the air needs to be released from under the tile. For a floor application, this is achieved by walking down the center of tiles lengthwise and stepping one foot in front of the other to cause equal adhesion of the tile to the substrate. For wall and countertop applications and rubber float or damp can be used to achieve the correct bond.The use of a vibrating machine is also part of the ANSI specifications. Once the first tile is in place and all excess thin set along with air has been released from under tile, the next tile is ready to be installed. Place the leveling spacers at least 8” from each corner and at 16” o.c. from those points. Prepare the second tile the same as the first once it’s in place and install repeating steps mentioned above.
Comb the thin-set using the notched side of your trowel, holding it at a 45 degree angle to the floor and lightly pushing the trowel teeth to the floor. Make sure you comb the thin-set in one direction. Avoid circular or swirling patterns.
Do not allow the thin-set to skim over or start drying as you go. If it does, remove it and apply new thin-set.
As you lay your Gauged porcelain, always check for dirt or dust. Wipe clean if needed. The dust can affect how effectively the tiles adhere to the mortar.
Throughout the process, use a damp sponge to clean off any mortar that ends up on top of the tiles. Do not let it dry. Once dry, mortar on the finished floor is extremely hard to remove.
If you need to take a break, always scrape up any mortar overlapping into an area you are about to tile. If left to dry, it will affect how well those new tiles adhere when you return to work those areas. Finish laying full tiles in your first quadrant. You’ll then be left with the space between those tiles and the wall where cut tiles are required. Finish laying all full tiles in your other three quadrants and let the mortar harden.
Now you’re ready to start cutting tiles. For this task, we recommend using a score cutter for straight cuts and an angle grinder with a diamond blade for curves and cutouts. A wet cut tile saw is recommended for cutting porcelain. Do not dry cut using motorized equipment due to the potential for exposure to harmful silica dust.
Measure the distance from the last piece of tile installed and the wall and deduct twice your grout joint size to allow for expansion joint along walls. Do this for all your cut pieces and start by cutting the largest sizes first to maximize your material. Once all cuts are made, install the same as you did the whole tiles.
The final step in tiling is applying grout. There are several types of grouts available in both sanded and non-sanded.
Make sure you purchased the correct type of grout. For joints 1/8 inch to ½ inch, use a sanded grout. For joints up to 1/8 inch and for all polished finish tiles, use a non-sanded grout. Follow your manufacturer’s mixing instructions.
Grout fills the spaces between the tiles. Use the grout coverage conversion charts on the back of the package to determine the amount of grout needed. And always wear rubber gloves and safety glasses when working with grout.
Before grouting, you must remove all of your tile spacers. Again, leaving the spacers in place and grouting over them will compromise the integrity of the grout. If you used the recommended leveling spacers, remove the wedge piece and snap off the space tower. You’ll also want to protect baseboards, trim and neighboring floors with painter’s tape.
Similar to thin-set, once the grout is mixed, allow it to stand for 10 minutes before applying. And avoid mixing too much grout at one time. Just mix enough for small sections until you become comfortable with the spreading process and can increase your speed.
Don’t forget to wear your safety glasses.
Spread grout in sweeping arcs with the rubber grout float held at a shallow angle. Apply at a 45 degree angle to the spaces between the tiles to prevent the float from pressing into the spaces and creating uneven grout surfaces. Press grout into the joints, filling them completely.
After the grout is spread, remove the excess with the grout float held at a 45 degree angle. Work diagonally across the joints to avoid dipping into the joints. The cement grout will set up in about five to 15 minutes and have a putty-like consistency.
As soon as you complete one section, take a damp sponge and do very light passes across the tiles diagonally to clean off the excess grout. Wring the sponge until no water drips from it before cleaning. Excess water can affect the consistency of the grout. Use both edges of each side of the sponge. Be careful not to press the sponge into the gaps. The drier the grout is on the tile surface, the harder it is to remove. Do as many passes as needed. The tiles won’t be clean on the first pass so just be patient.
Rinse the sponge frequently in clean water and change the rinse water frequently. The cleaner the water, the more effectively it will remove the grout from the surface of your tiles.
Remove any remaining haze by using an old T-shirt or cheesecloth. If you have trouble, try adding a grout haze remover solution. Try to remove all of the haze before it dries completely. Again, the drier it becomes, the harder it is to remove.
Help to slowly cure the grout by misting it twice a day for three days. Do not walk over the surface for eight to 12 hours to avoid getting debris and dirt in the grout lines.
Grout sealer provides unsurpassed, invisible protection for grout. Sealing your grout is critical to keeping grout lines clean and looking like new. Sealers help prevent stains, and keep mildew and mold from growing into the grout.
It’s easy to apply. You can choose a sealer with a built-in applicator or pick up a grout sealer application bottle.
Follow the manufacturer’s instructions on when to apply your sealer. In most cases, you’ll want to first allow the grout to cure for about three days.
Regardless of which you choose, you can expect your grout sealer to last an average of one to two years before needing to reapply it. To test, drop water on the grout. If it seems to soak in, it’s time to reseal.
To finish your project, remove the painter’s tape from any protected surfaces. Cover the expansion gap left along the walls. You can do this with either matching bullnose tile or wood quarter-round molding.
And finally, if you weren’t required to do so earlier in the process, now add any desired thresholds between your tiled floor and neighboring floors. And with that, your tile project is complete.
- Chalk line
- Safety glasses
- Rubber gloves
- Knee pads
- Buckets
- Drill and mixing paddle
- Spray bottle
- Zipper or Euro Notch Tile trowel
- Sponges
- Manual tile cutter (needs to be able to cut up to 126”)Blue Ripper straight cut rail system for cutting 12mm slabs.
- Angle Grinder with electro plated cutting blade
- Angle Grinder Miter Tool or Blue Ripper Miter Master (if doing mitered drop edge for countertop)
- Diamond Hole Saws (for plumbing fixtures and starting all interior cutouts)
- Glass suction cups (for handling and moving tiles)
- Stabilizer bar with suction cups
- Grout float
- Cheesecloth
- Respirator
MATERIALS:
- Stile® Porcelain Tiles
- Tile levelers and spacers
- Water
- Thin-set mortar
- Grout
- Painter’s tape
- Grout haze / film remover
- Grout sealer
- Paper towels
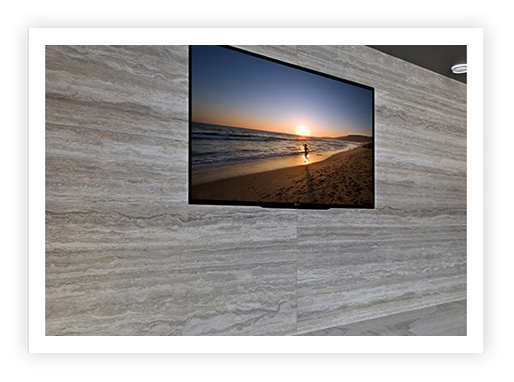
- Suitable for interior and exterior design projects.
- Quick installation over existing surfaces.
- Easier to cut, transport and install than natural stone.